Cuando el coche de Romain Grosjean se partió en dos y estalló en llamas durante el Gran Premio de Bahrein 2020, fue el Halo de titanio el que acabó salvándole la vida, pero lo que poca gente sabe es que una innovadora técnica de soldadura desempeñó un papel crucial para que ese elemento fuera lo suficientemente resistente como para funcionar tal y como se diseñó en aquel aterrador momento.
El Halo, ahora una parte esencial del paquete de seguridad de la Fórmula 1, se enfrentó a una fuerte oposición cuando se introdujo por primera vez en 2018. Sin embargo, varios accidentes de mucha espectacularidad, incluido el del francés, la dramática voltereta de Guanyu Zhou en el Gran Premio de Gran Bretaña 2022 y el choque entre Max Verstappen y Lewis Hamilton en el Gran Premio de Italia 2021, silenciaron a los críticos desde entonces. El dispositivo de protección del cockpit demostró su valía una y otra vez.
No obstante, lo que no mucha gente sabe es que fabricar el Halo para cumplir las normas de seguridad de la FIA. Para soportar las inmensas fuerzas a las que podría enfrentarse, tenía que ser capaz de soportar el peso de un autobús londinense de dos pisos, y supuso un gran desafío técnico, que los métodos de producción tradicionales no podían resolver. Para ello se necesitaba no solo titanio de alta calidad, sino también un proceso de soldadura impecable e innovador que preservara las propiedades del material.
El reto de soldar titanio del Halo para la F1
A finales de 2017, las empresas que participaron en la licitación de la FIA para la producción del Halo, incluida la parte que finalmente firmó el contrato, no tenían las capacidades técnicas internas para soldar las cinco partes de titanio con la máxima calidad posible. Fue entonces cuando recurrieron a LKN WeldTitan, la división especializada en titanio de la empresa neerlandesa, LKN WeldCompany BV.
Tras casi cuatro semanas de intensa investigación y desarrollo, consiguieron soldar las piezas de forma que se preservaran por completo las propiedades técnicas del titanio, garantizando que el Halo cumpliera las estrictas normas de la FIA, como explicó el fundador de la compañía, Patrick Wouterse, a Motorsport.com: “El titanio es un metal reactivo, lo que significa que reacciona con los elementos del aire, incluso a temperatura ambiente, en el sentido de que se produce oxidación. Por eso es muy resistente a la corrosión, una vez que se forma una fina capa de óxido, protege al metal de una mayor oxidación, una propiedad que hace que el titanio sea ideal para las industrias químicas”.
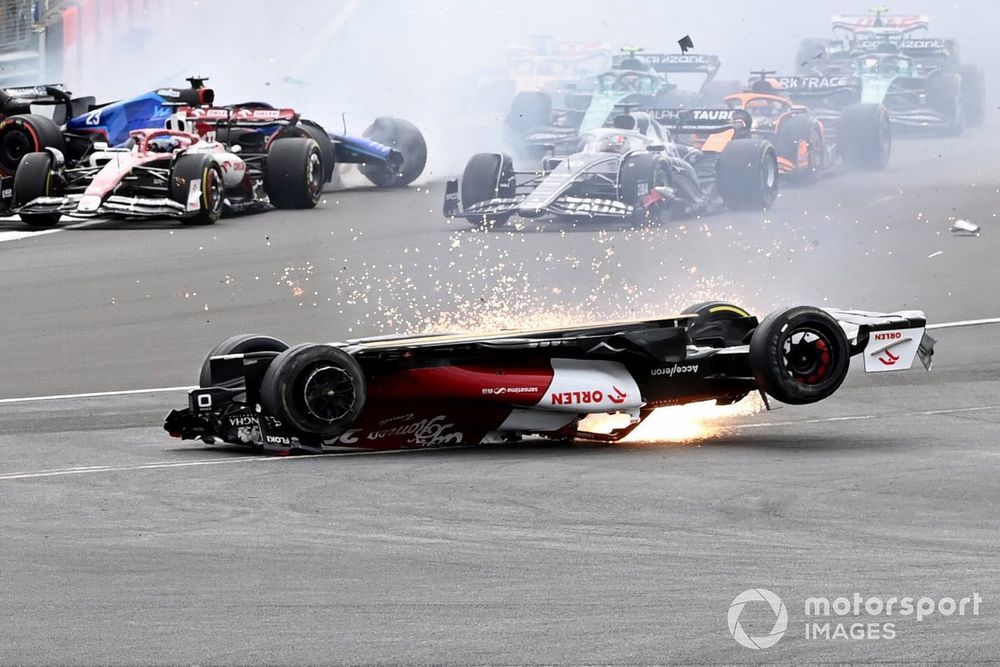
Sin embargo, para el Halo, la propiedad clave no era solo la resistencia a la corrosión, sino la relación resistencia-peso: “El titanio, especialmente la aleación de grado 5 utilizada para el Halo, es mucho más resistente que el acero y, al mismo tiempo, mucho más ligero. Para una determinada resistencia se necesitan 15 milímetros de acero inoxidable, pero solo 5 milímetros de titanio, por eso se utiliza tanto en la industria aeroespacial y se eligió para el Halo, quieres la estructura más resistente posible sin añadir demasiado peso al coche”.
No obstante, el titanio es un proceso delicado, ya que calentar el metal hace que se vuelva aún más reactivo, haciendo que absorba elementos como el oxígeno y el hidrógeno “como una esponja en un cubo de agua”. Incluso la más mínima contaminación, como restos microscópicos de suciedad o aceites procedentes de una huella dactilar, puede tener ya consecuencias desastrosas para la resistencia del titanio en la zona donde se encuentra la soldadura.
“Una vez que el titanio absorbe esos elementos, cambia la composición del metal y lo debilita drásticamente, hasta un 75% en la zona afectada”, explicó Patrick Wouterse. “Para evitarlo, hay que crear un entorno en el que, durante la soldadura, ningún otro elemento pueda llegar al metal”.
La innovación, un proceso de soldadura impecable dentro de una cámara de purga
Normalmente, los soldadores protegen la zona con un flujo local de gas inerte, como el argón, para blindar el metal fundido, pero con el titanio, eso no basta: “El calor se irradia hacia el exterior, el material circundante puede alcanzar los 1.000ºC, pero con solo 150ºC, el titanio ya empieza a absorber oxígeno”, continuó.
“El daño es visible, el titanio cambia de color. El plateado significa que las propiedades están intactas, mientras que el dorado indica que se ha producido un deterioro muy leve pero aceptable, pero si se vuelve azul, morado o verde, el material está arruinado”, aseguró Patrick Wouterse.
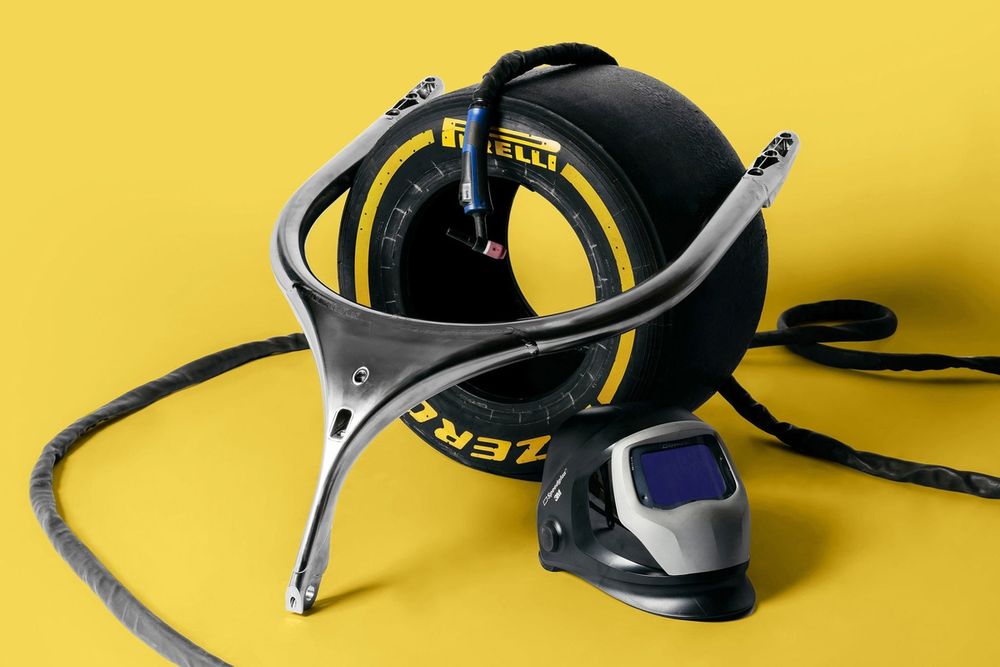
Para solucionarlo, él y su equipo pasaron años perfeccionando un proceso de soldadura único, construyendo cámaras de purga de soldadura especializadas, para que la soldadura pueda realizarse en una atmósfera de gas inerte: “Parece sencillo, basta con meter las piezas en una caja y llenarla de argón, pero es extremadamente complejo”.
El problema es que siempre queda una pequeña cantidad de oxígeno en la cámara de purga: “Llenamos la cámara principalmente con argón, helio y neón, pero el argón es pesado, el oxígeno es ligero y el helio aún más. Incluso la más mínima turbulencia al mover las manos dentro de los guantes puede mezclar los gases y elevar los niveles de oxígeno”.
“Tuvimos que encontrar la forma de reducir la concentración de oxígeno a unas pocas partes por millón”, continuó. “Todo, desde la forma de la cámara hasta el acabado de las paredes, afecta al resultado, así que todo eso es muy complicado, y hay al menos otras quince variables que tienen que ser perfectas para obtener los valores correctos”.
Digemaps alerta sobre fármacos para bajar de peso no aprobados por la FDA vendidos en RD
#Salud: Una mujer da a luz en el ataúd 10 días después de morir: ¿Qué sucedió?
Caribe Tours aclara videos sobre migrantes haitianos indocumentados
#Salud: Una influencer pierde a su bebé y una marca patrocinadora le pide devolver los artículos porque ya no creará contenido
#Salud: Cuidado, estos dos síntomas nocturnos podrían ser una advertencia de cáncer
En las dos últimas décadas, Patrick Wouterse se especializó en ese proceso. A través de LKN WeldCompany BV, se forjó una sólida reputación que dio lugar a una demanda mundial de la experiencia de su empresa en proyectos de soldadura especializada en sectores como el aeroespacial, energético, químico, nuclear, farmacéutico y automovilístico. Además, las empresas le contratan con frecuencia para el desarrollo de procesos y el control de calidad.
Después de que el proveedor del Halo de la FIA se pusiera en contacto con LKN a través de una conexión mutua, la empresa con sede en Amersfoort desarrolló una cámara de soldadura a medida lo suficientemente grande como para albergar toda la plantilla del Halo, teniendo en cuenta el complejo diseño hueco y asimétrico de la estructura.
“A continuación cualificamos el proceso según las normas EN ISO, soldamos un prototipo y lo probamos. Cumplía sin problemas las normas de la FIA”, recordaba Patrick Wouterse. “Después pasamos rápidamente a la producción. Acabamos soldando los primeros cien Halos para la Fórmula 1 a principios de 2018”.
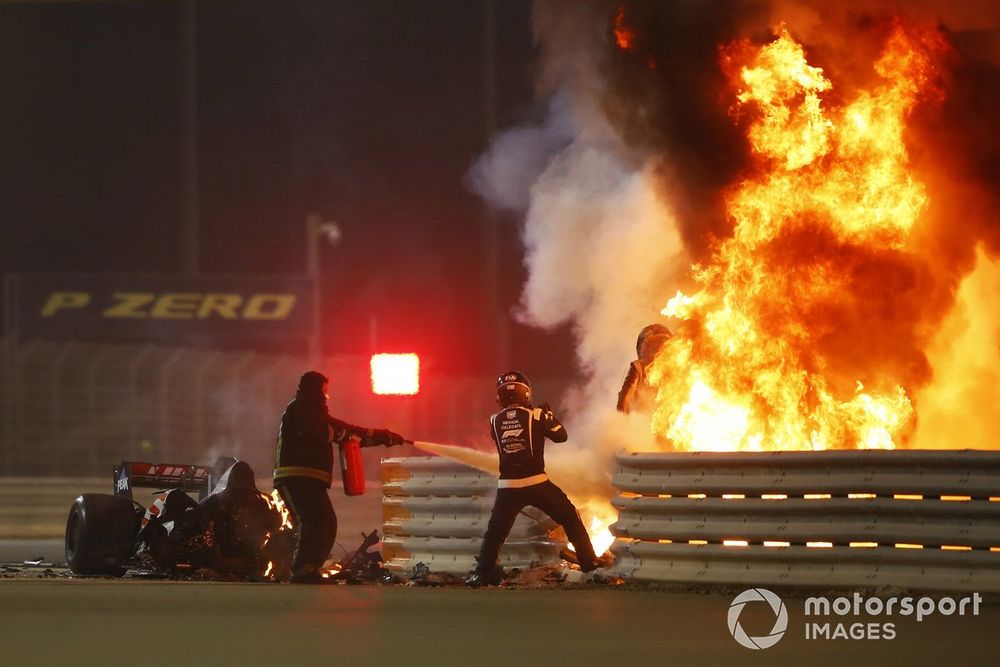
Un legado que salva vidas en F1
Para Patrick Wouterse, ver el Halo en acción, especialmente durante accidentes como el de Romain Grosjean, es una fuente de inmenso orgullo: “Siempre esperas que no ocurra nada malo, pero cuando pasa, es bueno saber que hay un Halo en ese coche, es un orgullo pensar, ‘hemos ayudado a hacerlo’. Sobre todo al principio, mucha gente odiaba el Halo, porque les parecía feo y algunos pilotos decían que les obstaculizaba la visión, pero después del primer gran accidente en el que marcó la diferencia, cesaron todas las críticas, todo el mundo estuvo de acuerdo en que era lo correcto”.
El accidente del galo dejó una impresión duradera en Patrick Wouterse: “Cuando miras las simulaciones que se hicieron después del incidente, ves cómo el Halo deformó la barrera lo justo para proteger la cabeza de Romain Grosjean. Sin él, no habría sobrevivido, y como el Halo aguantó, también pudo salir de los restos en llamas”.
Incluso intercambió mensajes con el piloto después: “Me puse en contacto en LinkedIn y le expliqué nuestro papel en el Halo. Me contestó, ‘entonces supongo que tengo que darte las gracias’, y como gran aficionado a la Fórmula 1 que soy, eso significó mucho”.
A finales de este año, planea visitar la Exposición de la Fórmula 1 de Ámsterdam para ver en persona el chasis quemado del francés, un poderoso recordatorio de la tecnología que salvó vidas y que él y su equipo ayudaron a perfeccionar.
¿Quieres leer nuestras noticias antes que nadie y de manera gratuita? Síguenos aquí en nuestro canal de Telegram y no te perderás nada. ¡Toda la información, al alcance de tu mano!
En este artículo
Sé el primero en enterarte y suscríbete para recibir actualizaciones por email de noticias en tiempo real sobre estos temas.
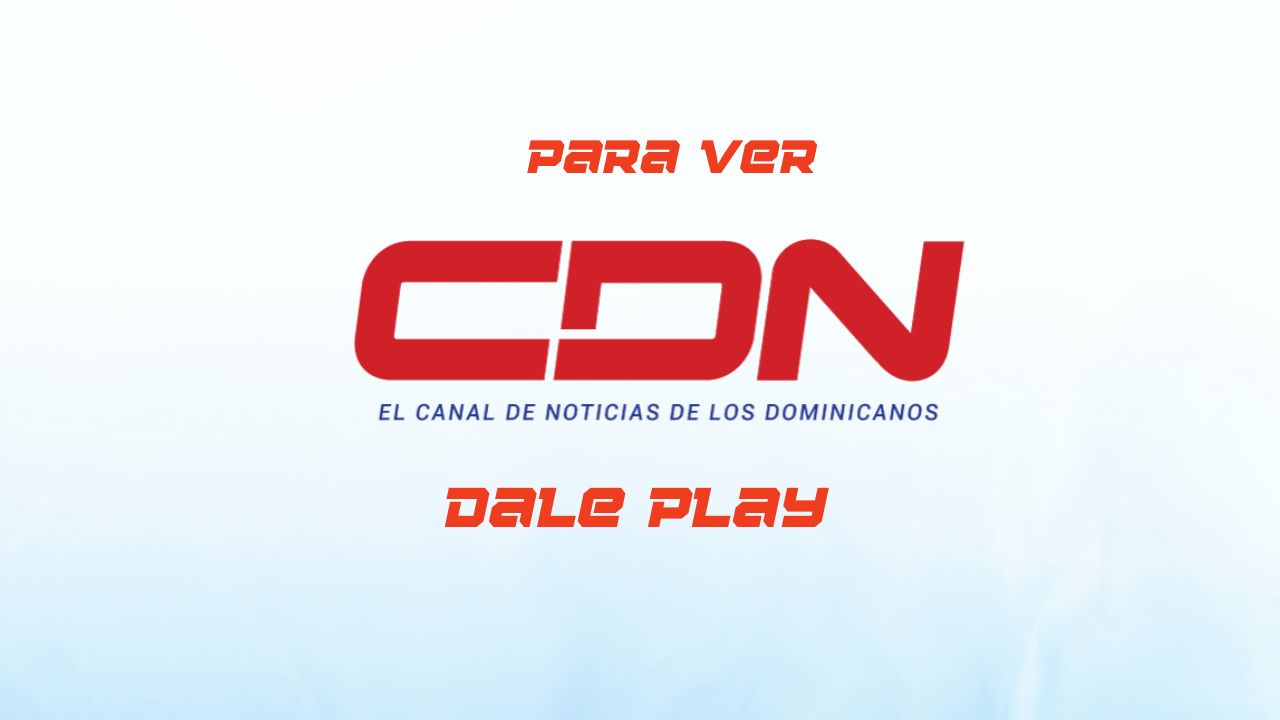